Post-tensioned bridges are a worry in particular. In post-tensioning, the space between the prestressed concrete steel tendons and the sheath surrounding them is filled with grout, which has the two functions of “attaching” and “preventing corrosion,” integrating with the main part of the concrete and enabling dynamically better behavior. Everyone thought passionately about “attaching,” but not as much about “preventing corrosion.”
Grout was used from about the 1960s, but because it was thought to be fine until the mid-1980s, no research and development on grout were conducted. Bad examples of this are the collapse of the Ynys-y-Gwas bridge in the United Kingdom in the mid-1980s and the prestressed concrete tendon ruptures in the Myōkō Bridge in the 2000s. According to a report, the UK bridge contained something like cardboard in the joints for some reason and deterioration began from there. However, nobody noticed and the bridge was used as normal until the collapse.
Case and interview
Dreams about infrastructure maintenance
We spoke to Senior Professor Toyoaki Miyagawa of the Unit for Infrastructure System Management Research, Center for the Promotion of Interdisciplinary Education and Research, Kyoto University, about the history of infrastructure maintenance and how Konica Minolta should aim to be in the future in order to contribute to the maintenance of infrastructure in society.
Building and checking. Both of these wheels are essential for infrastructure maintenance.
› Tell us about your attitude to the challenges regarding the aging of Japan’s infrastructure.
Much of Japan’s infrastructure was constructed during the postwar period of high economic growth. Normally, depreciation or some other form of a decrease in value should have been included in advance, but it was built without thinking about that. However, they knew that it would deteriorate in many different forms once 50 or 100 years pass, actually. Then, we have to come up with the costs to maintain it in some other form. When this becomes too much, civil society breaks down. To live sustainably, richly, and securely, it is necessary to manage infrastructure well.
Moreover, infrastructure is, in the first place, something that supports civil society, and if concrete structures are not strong, beautiful, and long-lasting, they will end up overturning civil society. From either aspect, we can conclude that infrastructure maintenance is important. When maintaining, the key is to have both “technology to create” and “technology to use,” as in the diagram on the right. New buildings require testing, which allows proper creation while existing buildings require diagnosis, which leads to proper use. The act of building often attracts the spotlight while the act of checking does not, but if we do not both “build” and “check,” we cannot “properly create” and “properly use” various structures.
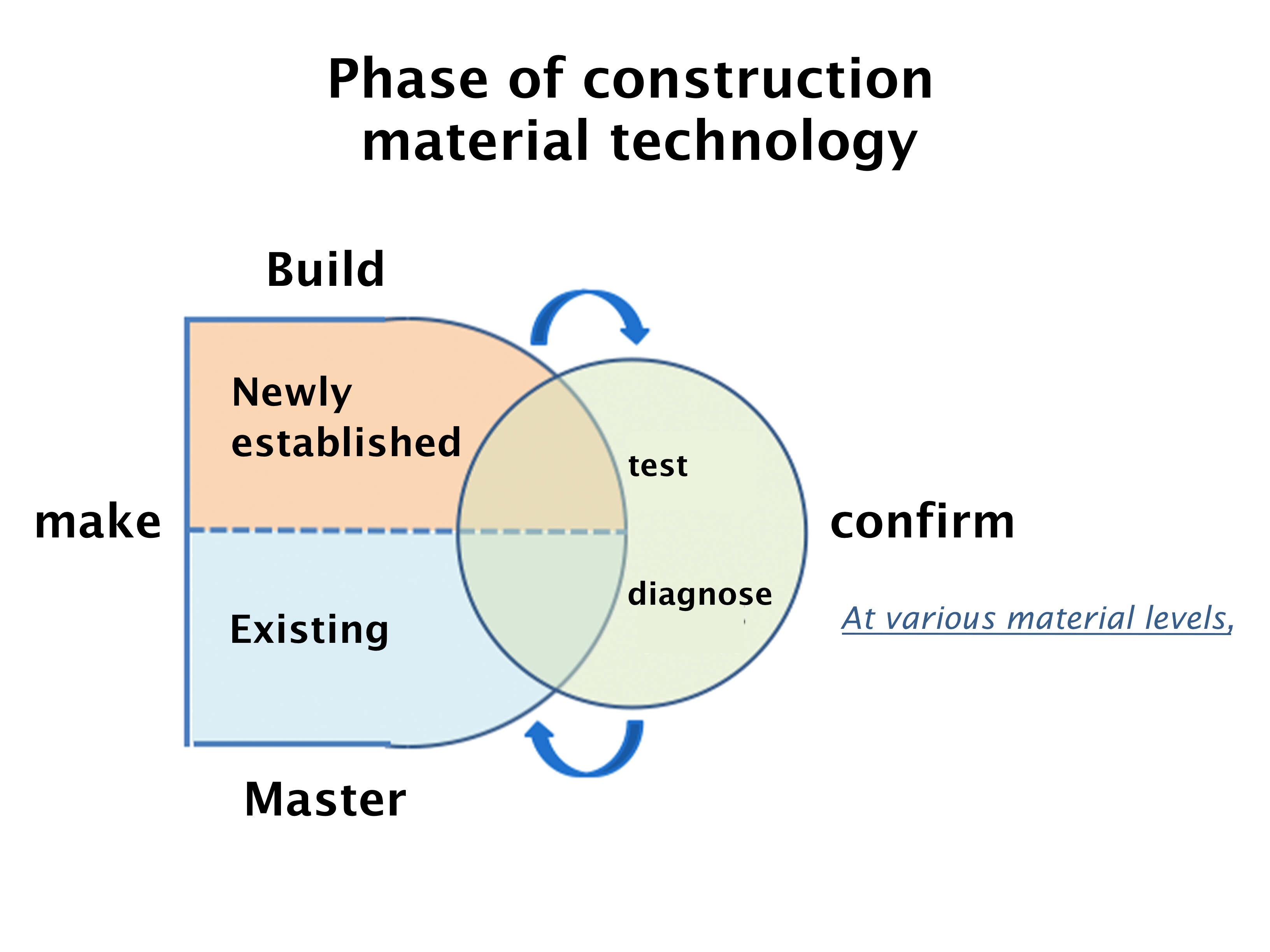
Flux leakage method, which allows non-destructive detection of internal tendon ruptures
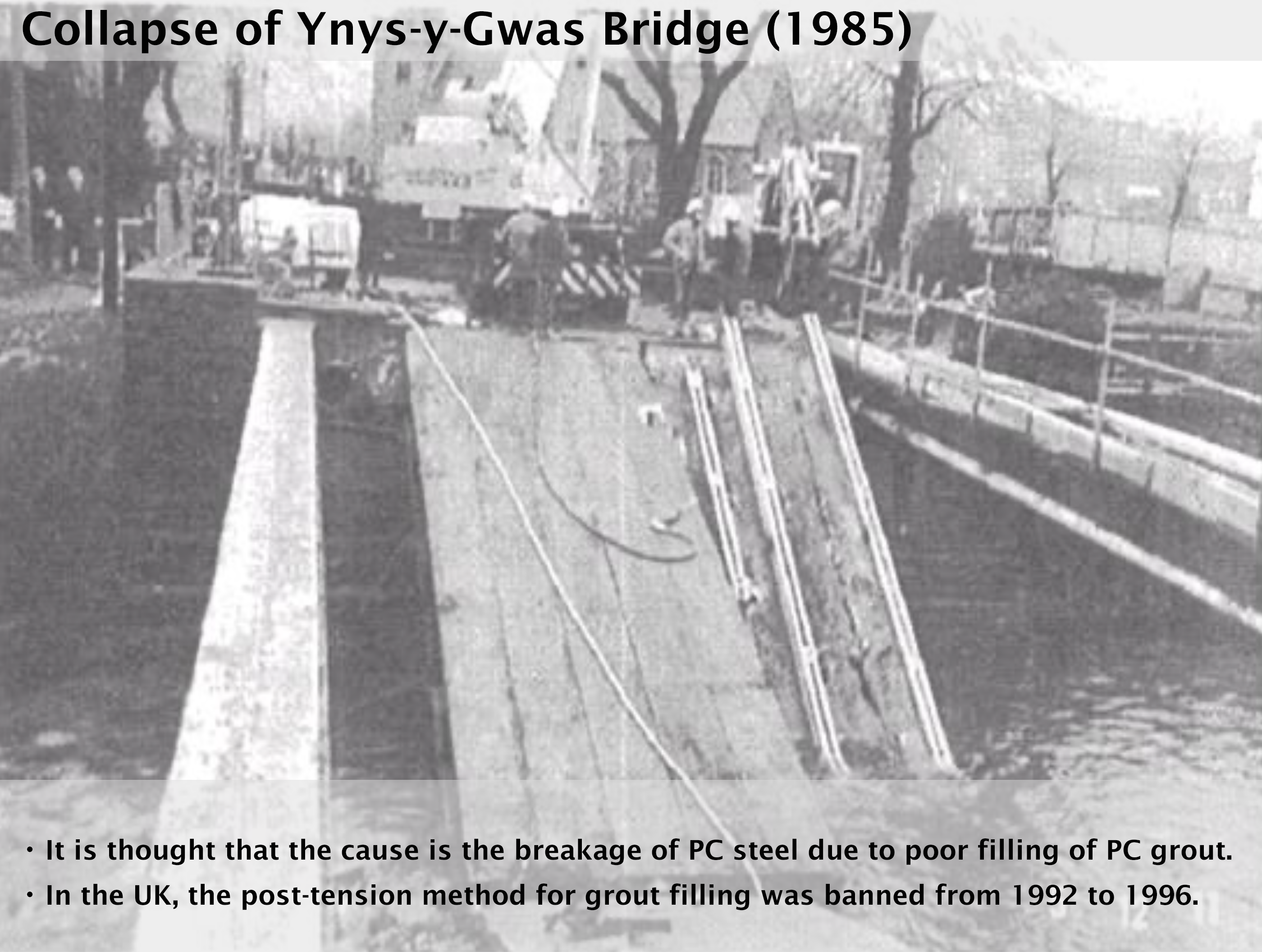
One of these “checking” acts is diagnostic technology for tendon ruptures in prestressed concrete. With normal reinforced concrete, there is nothing to worry about even with considerable deterioration, and some bridges manage to hold on even if the rebar is hanging down, but prestressed concrete bridges may collapse if the tendons corrode and rupture. The first event to cause shock in Japan was the collapse of the Ynys-y-Gwas bridge in the United Kingdom.
Long ago, prestressed concrete was supposed to have excellent durability. High strength and high durability—it was thought to be good because it prevented cracks due to prestressing. That is certainly true. However, the most important part (rupturing in the prestressed concrete tendons) has not been sufficiently considered.
Structures built in the 21st century are reliable, but prestressed concrete structures built in the 20th century have been held to have faulty grout. Given this, we searched for various testing technologies. One was a test to see whether the grout had been filled properly, and another was a test to see whether the prestressed concrete tendons had no abnormalities.
For grout filling, researchers developed the hammering vibration method, as well as X-ray radiographic inspection, the broadband ultrasound method, and other methods.
Existing non-destructive inspection

However, as there is no problem if there is no corrosion, even with no grout at all, we searched for technologies for the prestressed concrete tendons, which is what we really wanted to know about. What we found was the flux leakage method. I first learned about the flux leakage method over 20 years ago, I think. The first opportunity was when someone mentioned that you could immediately see tendon ruptures in prestressed concrete on utility poles. Next, it was applied to look at ruptures with ASR, and after that, it was applied to ruptures in prestressed concrete tendons.
The flux leakage method uses the magnetic field leaking from magnetized tendons to enable non-destructive detection of ruptures in prestressed concrete tendons. SenrigaN is a unique technology that is also capable of detecting tendon ruptures by the flux leakage method and a method that applies it and that can detect ruptures even in thick tendons, which are difficult to magnetize. With its ability to show results immediately, I think it is easy to use on site as well.
Considering the future of infrastructure maintenance, non-destructive testing of the interior of concrete is a challenge that the entire industry should work on. For example, the flux leakage method can show tendon ruptures, but in truth, knowing about the stage before this would be better. Is there any corrosive deterioration? Have any cross-section losses occurred? These are what lead to ruptures. I look forward to progress in this area, too.
› I am sometimes asked by bridge maintenance staff whether the tendons really rupture.
We also have not seen a case of a rupture very many times. But it is certain that tendons rupture, and we need to appreciate that the effects when tendon ruptures are severe.
I have been involved in formulating policies and guidelines for appropriate maintenance. To date, I have organized the Prestressed Concrete Durability Improvement Manual (November 2000), which is a standard that covers both durability and maintenance for prestressed concrete structures, as chief of the Durability Improvement Subcommittee in the Prestressed Concrete Technical Standards Research Committee in the then-Japan Prestressed Concrete Engineering Association, which has now been renamed the Japan Prestressed Concrete Institute. At the time, I did not write much about grout. We had little awareness of it as a problem, and there was not enough information to write about it.
Later, I published Guidelines for Examination, Repair, and Reinforcement Prestressed Concrete Tendons in Existing Post-tensioning Bridges (September 2019), a guide targeting prestressed concrete grouting and steel ruptures, through the Japan Prestressed Concrete Institute. As the chair of the Committee on Responses to Prestressed Concrete Grouting Issues in Existing Post-tensioned Bridges, I organized the guide with Aoki Keiichi and Hagiwara Naoki of the Nippon Expressway (NEXCO) Research Institute. The Committee on Responses to Prestressed Concrete Grouting Issues in Existing Post-tensioned Bridges was the Japan Prestressed Concrete Institute’s first large-scale committee that included members from MLIT, expressway companies, various JR companies, and local public entities. The committee created various materials, and in that process, I became closely involved with the flux leakage method again, which led to the creation of the Prestressed Concrete Tendon Non-destructive Testing Association.
Not much research is conducted on prestressed concrete tendon rupturing, even in other countries. It is fair to assume that the Prestressed Concrete Tendon Non-destructive Testing Association and Konica Minolta are the leading edges.
You cannot ask for 100% with non-destructive testing. Understanding the errors and using it properly is key.
› How should non-destructive testing develop?
I believe that you cannot ask for 100% accuracy with non-destructive testing. The key is to use it appropriately, based on the errors in it. In the first place, the owner should indicate that they “demand non-destructive testing capable of detecting something of this level,” but I do not think that is happening.
Even when they want to know whether the prestressed concrete tendons are corroded, they are not clear about the degree of corrosion or rupture that they want to know about, and it is not clear yet what degree of rupture is not good.
So, what is of greatest concern in my discussions with NEXCO, JR, and others are non-destructive testing, and the reality is that there is no technology that truly hits the mark. This is an area that still needs a lot of research and development, where the scope of the market is extremely broad. It is not realistic for a single company somewhere to cover from Hokkaido to Okinawa. I thought that experts have to collaborate from a range of perspectives, which led to forming the Prestressed Concrete Tendon Non-destructive Testing Association. The proportion of revenue that companies in the construction industry spend on research and development is small, amount to about 1% in large-scale general construction companies. Rather than one company seeking to do it alone with just its unique technology, I think it would be better for them all to cooperate and collaborate. Please use the Prestressed Concrete Tendon Non-destructive Testing Association for this purpose. The civil engineering industry does not have detailed knowledge about fields like electricity and magnetism, so I think it would be good for them to provide topics for discussion in training or similar.
› If measuring the entire bridge is not practical in terms of expense or time, where should I measure it?
At the moment, if there are cracks in a shape that seems to follow the prestressed concrete tendons, I suggest measuring that part. We do not really know why it happens that way, but it is fairly common for cracks to form when the grout is not properly filled. You also need to measure places where there is clear salt damage, such as effects from antifreeze agents. Alternatively, if you are using inspection results, it is important to take an approach like identifying “bridges with an upper edge anchoring structure” that were built in the 20th century as the scope, or using an insufficient filling risk chart for screening, for example. These kinds of things are suggested in the Japan Prestressed Concrete Institute guidelines.
› Are you considering having detailed testing methods added to the statutory inspections, or something like that?
Regular inspections and detailed testing are of a different character. Detailed inspections ask you to consult an expert if there is an abnormality.
Expressways and JR carry out large-scale renewals. They carry out various considerations linked to those, and I think they definitely need to debate things like this within these considerations.
› What are your expectations for non-destructive testing for prestressed concrete tendons in the future?
In concrete structure and infrastructure, “what is wrong now” and “what will go wrong in the future” are different. The flux leakage method in its current state is a technology for diagnosing present ruptures, but it would be great if we could use it to infer future ruptures, including corrosion, rust, and cracks so that we could look at the current state and infer how it might corrode in future. Doing this requires us to accumulate data from now.
›I hope that we can be play a role in infrastructure maintenance while cooperating with everyone in the industry.
Thank you for your valuable discussion today.
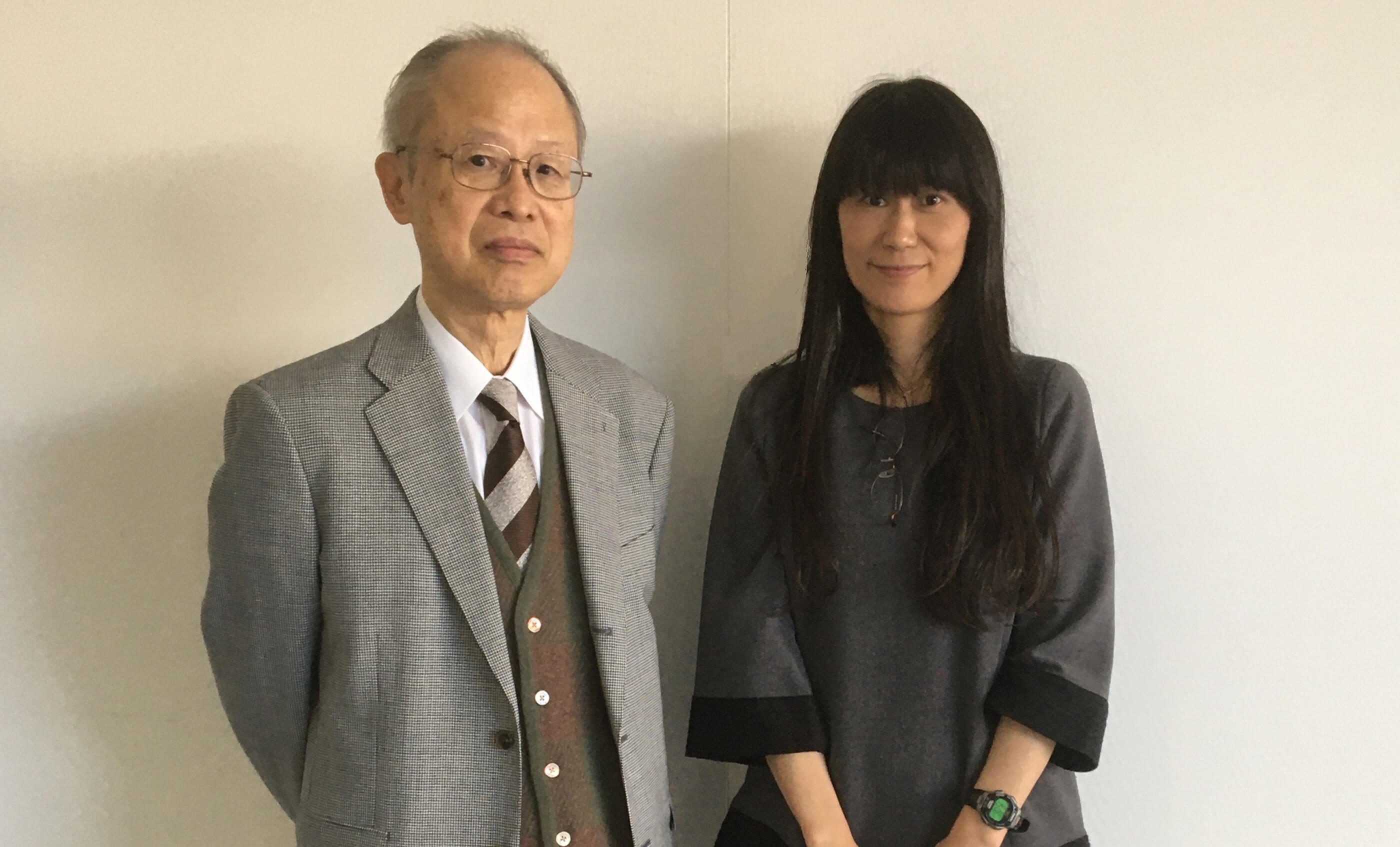
Kyoto University
Toyoaki Miyagawa, Senior Professor
BIC-Japan, Konica Minolta, Inc.
Noriko Ōhara